The forging industry requires the highest standards of quality and precision to produce the best gears, components, and equipment for various applications. With the help of cutting-edge technologies like 3D scanning, quality control and inspection, forging companies can ensure they produce high-quality products with accuracy.
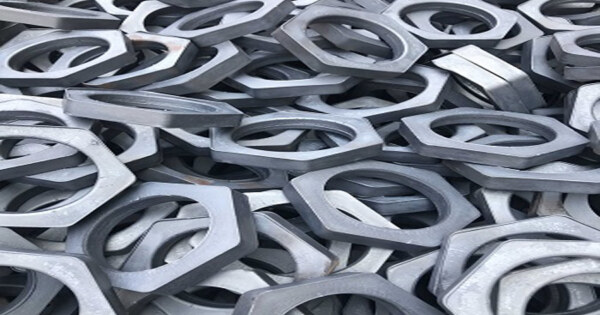
In this blog, we'll explore how industry-leading portable 3D scanning technology can help forging companies measure equipment and finished products with accuracy and precision. We'll also dive into some quality control and inspection techniques that can help ensure top-quality products in any forging process.
Precision Forging Gear Basics
Before we dive into how portable 3D scanning technology can benefit the forging industry, let's first explore what precision forging gear is all about. Precision forging is the process of creating complex, high-precision gears and components that require tight dimensional tolerances and straightness. The forging process involves the application of pressure and heat to shape and deform metal blanks into final product shapes.
By using precision forging techniques, companies can produce stable and reliable products that meet the needs of various industries. The forging process ensures these products have high strength, thermal stability, and corrosion resistance, making them ideal for applications in aerospace, automotive, oil and gas, and other industries.
Precision forging gear is critical for quality products because it ensures the stability and accuracy of the final product. Even the slightest deviation from the intended design can have a significant impact on the product's functionality and longevity. Thus, top-quality production requires meticulous attention to detail in the design and manufacturing process.
Portable 3D Scanning Technology for Quality Control and Inspection
In the forging process, quality control and inspection are essential in ensuring high product quality. With portable 3D scanning technology, forging companies can measure equipment and finished products with accuracy and precision.
Portable 3D scanners are a game-changer in the quality control and inspection process. They allow technicians and engineers to quickly capture data on various parts and equipment, providing real-time feedback on the manufacturing process's quality.
FARO's 3D scanning technology, for example, provides accuracy and precision in measuring critical parts using laser scanning capabilities. Portable 3D scanners offer improved accuracy, speed, and repeatability of measurements, making them ideal for critical applications like analyzing gear teeth.
With 3D scanning, it's easier to identify issues early on in the manufacturing process, saving time and preventing costly mistakes. Technicians can also use the data captured from 3D scanning to refine the manufacturing process and make improvements to ensure top-quality products.
Quality Control and Inspection Techniques
In addition to using portable 3D scanning technology, quality control and inspection techniques are essential in ensuring the highest product quality. Here are some techniques that can be used in the forging process:
1. Sample testing: This involves selecting a sample from a lot to test its properties. This technique helps to identify any defects or variations in the manufacturing process and allows companies to refine their production process as needed.
2. Statistical process control: This technique involves monitoring the forging process's variables, such as temperature, pressure, and speed, to identify any deviations from the intended design. Using statistical methods, companies can analyze data from the forging process to ensure the process remains within acceptable limits.
3. Non-destructive testing: This technique involves the use of ultrasonic, magnetic, or visual inspection to detect any defects or faults in the final products without damaging them. Non-destructive testing provides a quick way to ensure product quality and identify any issues that may have gone unnoticed during the manufacturing process.
Conclusion
Precision forging gear is essential in ensuring high-quality and reliable products. With portable 3D scanning technology and quality control and inspection techniques like sample testing, statistical process control, and non-destructive testing, forging companies can ensure top-quality products that meet the needs of various industries.
Investing in advanced technologies and adopting a quality-focused approach to production is critical in today's forging industry. Companies that prioritize quality control and use the latest technologies like 3D scanning are likely to stay ahead of the competition and provide customers with the best products available.