Precision Grinding, Customizable Machine Solutions, High-Precision Grinding
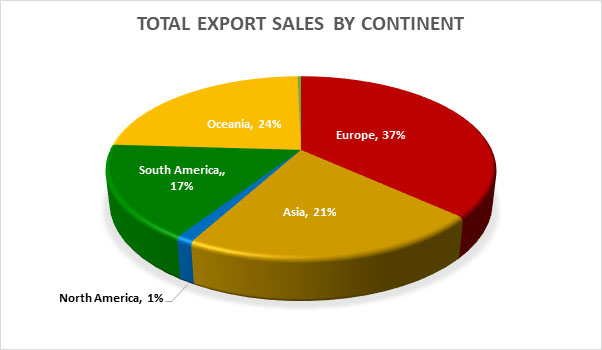
Sintered components have become an essential part of modern engineering as they possess unique features that help in increasing the efficiency and durability of the final products. These components, made by pressing powdered metals under high pressure and temperature, require precision grinding to achieve the desired shape, size, and finish. The process of grinding sintered components needs to be accurate, reliable, and efficient, keeping in mind the specific requirements of the industry. In this blog, we will discuss the importance of precision grinding for sintered components and how customizable machine solutions can enhance the process's overall efficiency.
High-Precision Grinding for Sintered Components
Precision grinding is the process of removing material from a workpiece to achieve a precise size and shape. It is crucial in the manufacturing process of sintered components as they need to meet stringent quality standards. Precision grinding can be performed using different techniques, such as surface, centerless, ID/OD, and creep-feed grinding. Among these, centerless grinding is commonly used for sintered components as it allows for precision grinding without causing deformation in the material.
The benefits of precision grinding for sintered components are numerous. It helps to achieve tight tolerances and surface finishes, ensuring that the components fit perfectly into their designated position. Precision grinding also eliminates defects, such as cracks or burrs, that may impact the component's functionality or overall product quality. The process of grinding sintered components enhances the durability and longevity of the final product while reducing costs associated with maintenance and repair.
Customizable Machine Solutions for Precision Grinding
Customizable machine solutions have revolutionized the precision grinding process for sintered components. These machines are designed to meet the specific needs of the industry, ensuring that the grinding process remains accurate, reliable, and efficient. Customizable machine solutions offer flexibility, enabling manufacturers to modify machine settings for different components, materials, and quantities. The modular design of the machine allows for easy integration of additional components, making it a cost-effective solution for manufacturing sintered components.
Customizable machine solutions have several benefits over standard machines. They can be tailored to meet industry-specific requirements, such as size, shape, and surface finish. These machines have automated features, ensuring consistent quality products and reducing human error. Another significant advantage of customizable machine solutions is their ability to reduce the lead time for manufacturing sintered components. They offer high-speed grinding capabilities, enabling manufacturers to produce components in large quantities quickly.
Conclusion
Precision grinding is an essential process for manufacturing sintered components. It helps to achieve tight tolerances, eliminate defects, and enhance the durability of the final product. Customizable machine solutions have significantly improved the precision grinding process by offering flexibility, automation, and high-speed capabilities. The ability to customize machine solutions to meet industry-specific requirements has reduced costs associated with maintenance, repair, and lead times. Therefore, if you are an OEM sintered components manufacturer, it is essential to invest in high-precision grinding machines that can be tailored to your specific needs.