Powder Metallurgy (PM) refers to the process of making metal parts using powdered metals. Powder metallurgy parts are popularly utilized in various industrial applications due to their unique characteristics such as high cohesiveness, uniformity, and strength. Powder metallurgy is an extremely efficient method of producing parts because it eliminates the needs for multiple processing stages such as melting, casting, and machining. This article highlights the importance and benefits of powder metallurgy parts, including their applications, advantages, and market trends.
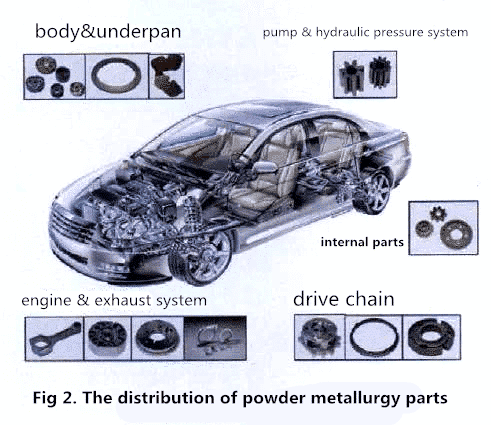
Applications of Powder Metallurgy Parts
Powder metallurgy parts are widely used in various industries, including automotive, aerospace, medical, and electronics. Automotive manufacturers incorporate powder metallurgy parts in engines, transmissions, and brake systems due to their strength, resistance to wear, and better efficiency. In the aerospace industry, powder metallurgy parts are used in engines, landing gear, and wings due to their high-temperature resistance and superior strength. In the medical sector, powder metallurgy parts are used in implantable medical devices due to their biocompatibility and ability to withstand body fluids. The electronics industry utilizes powder metallurgy parts in conducting materials, sensors, and radiation shields due to their electromagnetic properties.
Advantages of Powder Metallurgy Parts
Powder metallurgy parts offer significant advantages compared to traditional metal fabrication techniques. The following are the most prominent benefits of powder metallurgy parts:
1. Cost-efficiency: Powder metallurgy parts production is an efficient and cost-effective method of making metal parts compared to traditional manufacturing techniques.
2. Reduced waste: Powder metallurgy parts use about 97-99% of the raw materials, while traditional techniques like casting discard about 40% of materials as scrap.
3. Precision: Powder metallurgy parts manufacture procedures enable the fabrication of complex and intricate parts with tight tolerances and dimensional accuracy.
4. Customization: Powder metallurgy parts allow for customization to specific end-use applications with tailored shapes, sizes, and surface features.
Market Trends of Powder Metallurgy Parts
Powder metallurgy parts market is experiencing a steady growth rate due to the increasing demand for crafted, specialized, and efficient products. The global powder metallurgy parts market is projected to reach USD 15.7 billion by 2025, growing at a CAGR of 4.8%. The rise in the consumption is attributed to the expanding demand from the transportation, electronics, and medical sectors. The Asia-Pacific region is projected to exhibit the highest growth rate during the forecast period, primarily due to the growing population, rising disposable income, and increased demand for lightweight and fuel-efficient vehicles.
Conclusion
Powder metallurgy parts offer a cost-efficiency, waste reduction, precision, and customization advantages compared to traditional metal fabrication techniques. The increasing demand from the transportation, electronics, and medical sectors drives the growth of the global powder metallurgy parts market. The Asia-Pacific region is expected to experience the highest growth rate during the forecast period. Therefore, it is crucial for metal fabrication industries to leverage the advantages offered by powder metallurgy parts and to adopt the technology to remain competitive in the market.